Laboratory plant engineering system test (LAST)
The demands on today’s automation technology are constantly increasing. Hardware components, cables and communication software should convert data faster and faster and still remain inexpensive and compatible.
In order to work on efficient solutions for these challenges, we have set up several modular test stands in our laboratory at the OTH Amberg.
KoBus/KoBa cable system
In the “KOBA” project, the possibility of an advanced plug-free but wire-like backbone system for modular automation technology components was examined and set up as a demonstrator. The way in which this can be implemented for a decentralized arrangement in the field was also shown. For these fields of application, an efficient, inductive energy coupling method should be implemented as well as plug-free, robust and reliable data transmission with a high data rate but short range. The project was funded by the State of Bavaria.
In the “KoBus” project (contactless bus system), a new type of contactless bus system was developed for the joint transmission of energy and data at the field level. The system based on inductive transmission should offer the already known advantages of contactless transmission such as high flexibility, low maintenance requirements and resistance to corrosion, while supplying a large number of consumers not only with energy but also with data.
Other topics dealt with around contactless energy and data transmission are the design and experimental setup of pads for charging electric vehicles, various RFID applications and the contactless variant of GreenPHY communication.
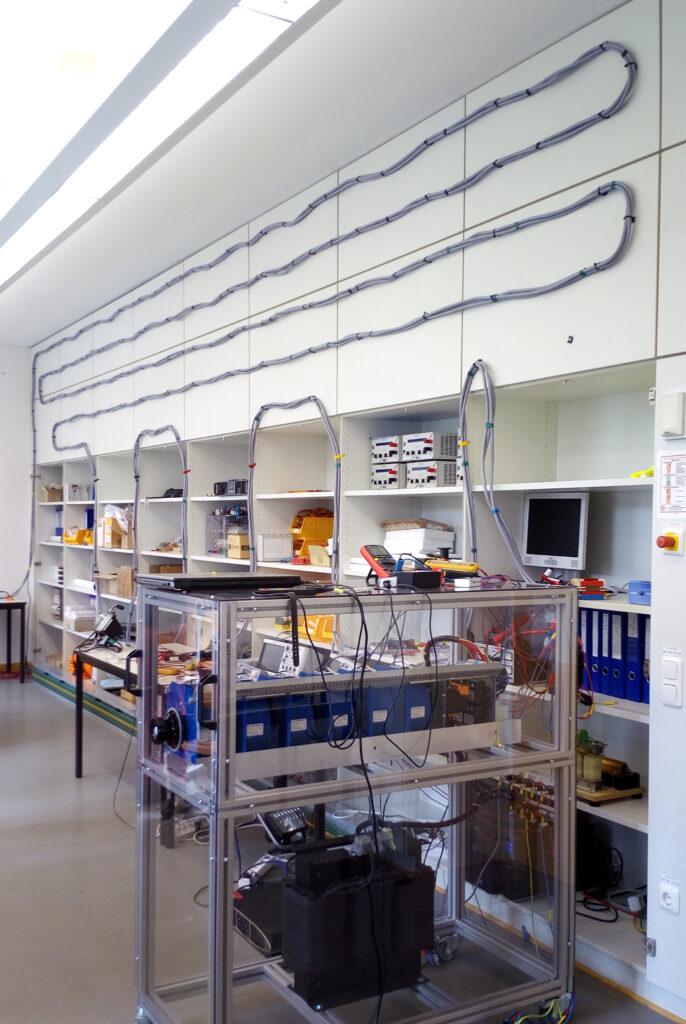
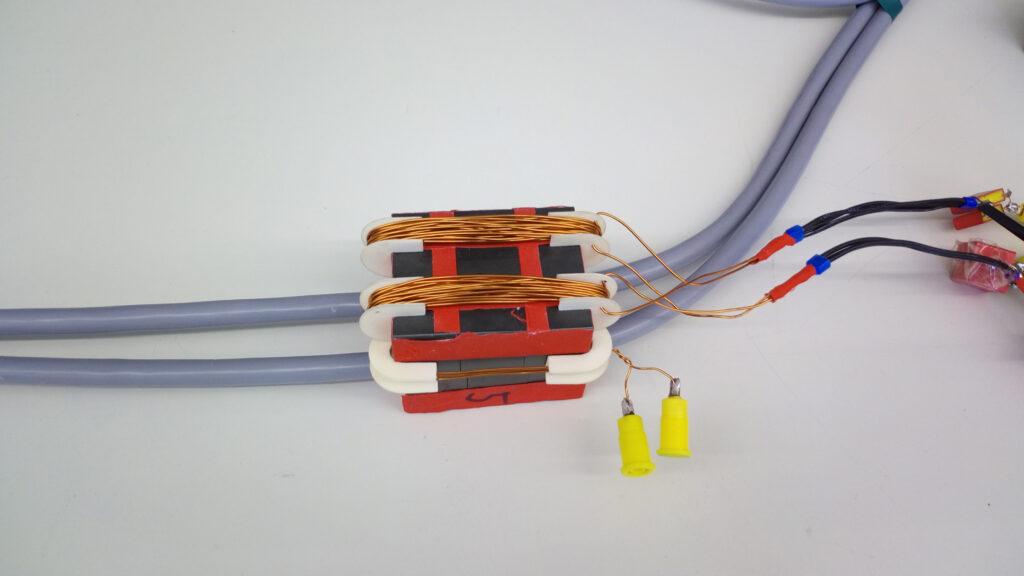
The Smart Factory Demonstrator
A number of test stands were designed for the interdisciplinary ISAC project to simulate a fully automated process chain in an industrial plant. These include several conveyor belts, motor stands with load simulators and communication components for Industry 4.0 systems. With this series of simulations, a product is to be automatically processed and transported to a storage system.
The special feature of this Industry 4.0 demonstrator is its modular design. Eight independent conveyor modules form the basis of the demonstrator. The modules recognize each other via RFID. Thanks to the modular design and mutual “neighbourhood recognition” of the individual modules, this system can be rearranged during operation without the individual “production steps” of the workpieces getting mixed up. The eight modules are organised into two groups. Modules 1–4 are transverse conveyors. They have no sensors, but a turntable that enables conveyance in three different directions. Modules 5–8 have sensors/actuators. Here the physical data of the cans can be read and “processing” can take place.
Furthermore, an engine test bench consisting of an ASM and a servomotor is installed in modules 6 and 8. They not only generate realistic malfunctions on the data line, but also dynamically transmit the current measured values (rotation rate, rotation direction, torque) to the PLC and display them on the HMI. These engines are currently under construction.
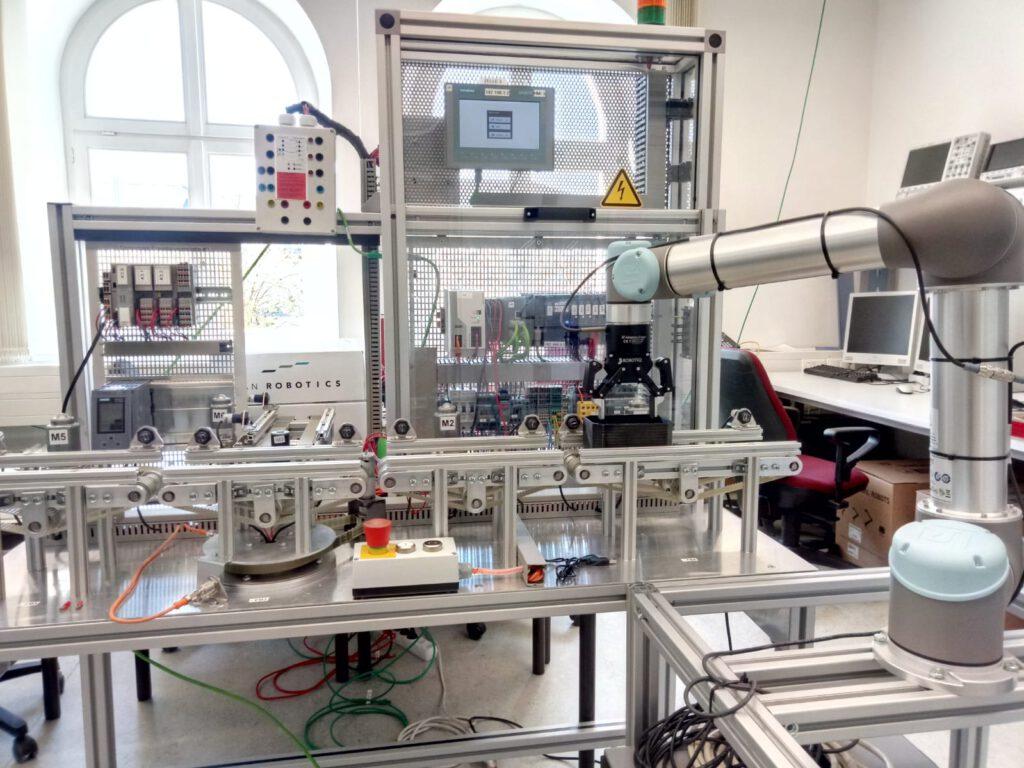
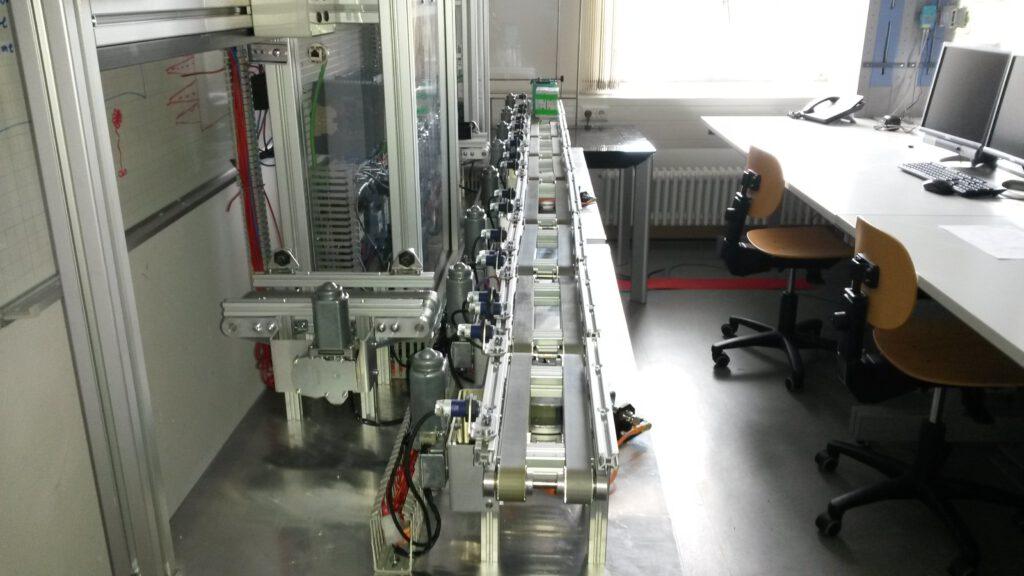
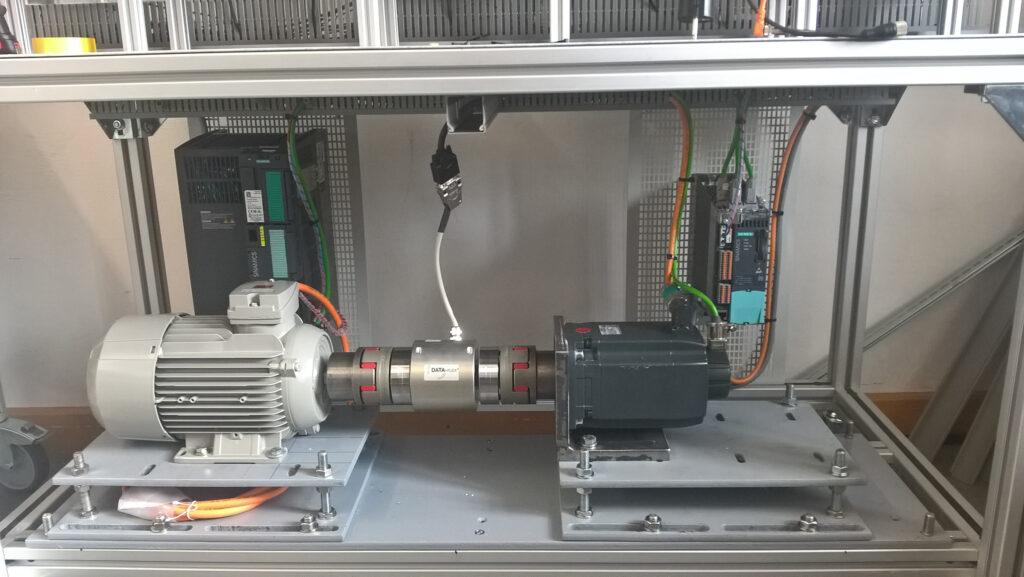
Industrial Communication Technology and Automation Systems
The lectures give students an insight into process automation and the required components and systems.
Communication systems for process data transmission (PROFINET, Ethernet, etc.) as well as real-time operating systems and real-time applications for process control are dealt with.
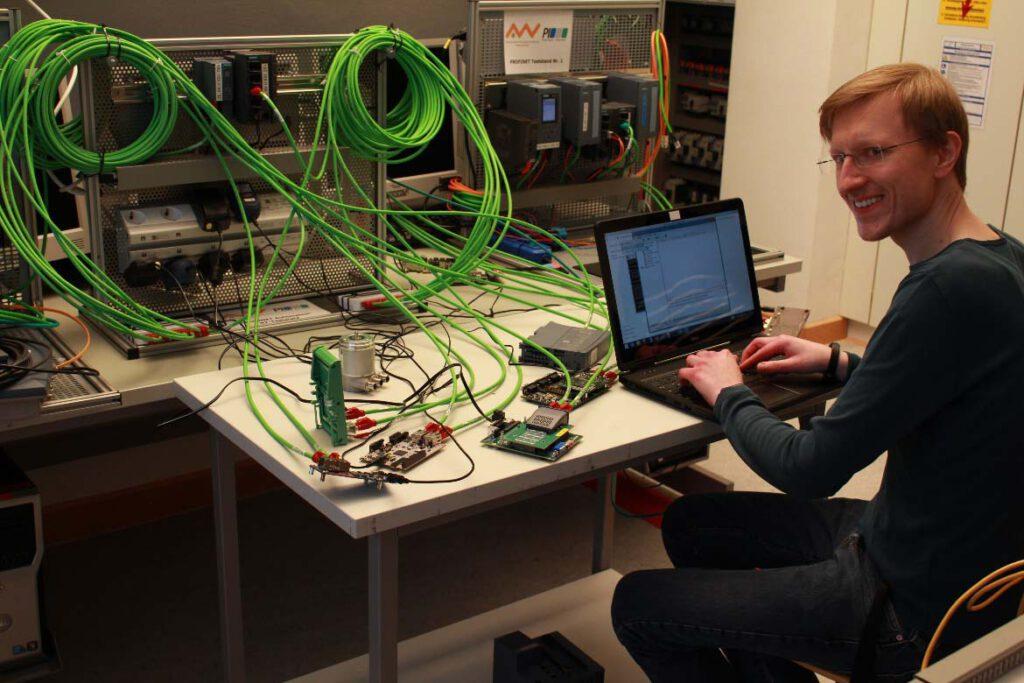