Industrial Ethernet PROFINET
PROFINET certification.
PROFINET certification
PROFINET is one of the leading industrial Ethernet standards. It is distributed worldwide and has established itself as the market leader in numerous industrial sectors. The AUT working group of OTH Amberg-Weiden and the aia (automations institut amberg) develop and maintain the Automated RT-Tester in close cooperation with major manufacturers and users. The Automated RT-Tester is a system that is used worldwide for the certification of PROFINET devices in order to ensure compliance with the highest quality requirements.
PI (PROFINET & PROFIBUS International) maintains a worldwide network of accredited test laboratories in which manufacturers of PROFINET components can have the behaviour of their products tested and certified in precisely defined structures by means of the Automated RT-Tester. The test software currently already covers more than 80% of PROFINET basic specification.
The expansion of the test scope is particularly interesting: while thus far only PROFINET devices have been certified with the Automated RT-Tester, in future there will also be tailored test cases for controllers. The PROFINET provider-consumer model and the associated division into active and passive components places particular demands upon the test software. The AUT working group is also heavily involved in the development of test standards and test software in this field.
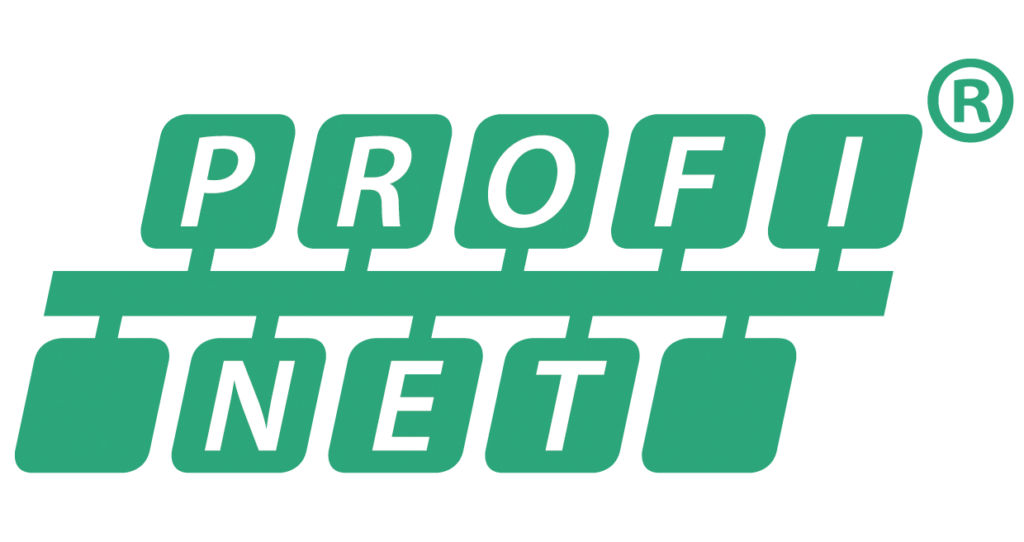
PROFINET Automated RT-Tester
In order to meet the constantly increasing requirements of the industry, the open PROFINET standard is constantly the subject of efforts for expansion and further development. The widespread use of PROFINET makes the standard interesting not only for the various industrial users, but also for a large number of device manufacturers. Against the backdrop of the resulting variety of devices, various quality assurance mechanisms were established early on, one of which is the certification process for PROFINET devices.
To ensure the interoperability of devices from different manufacturers, PI (PROFIBUS & PROFINET International) has initiated an extensive certification programme. Every PROFINET device must be successfully tested by an accredited test laboratory before the manufacturer receives the corresponding certificate from PI. Such a test procedure comprises a sequence of precisely defined test cases in which a device’s various functions are examined. Thus, an official PROFINET certificate guarantees absolute compatibility with other PROFINET products.
The test cases are carried out using a special software: the Automated RT-Tester. It is being developed for the PNO at the OTH Amberg-Weiden at the Amberg site by the AUT working group with the support of the aia – automations institut amberg.
PROFINET device certification:
The AUT working group has been working on the implementation of the Automated RT-Tester for the certification of PROFINET devices since 2014. The functionality of the test software has been gradually expanded and now covers approximately 80% of the PROFINET basic specification. The majority of test cases that were previously carried out manually in the test laboratories have now been automated and integrated into the test software. In addition to its use in certification, the Automated RT-Tester is also used by various PNO companies in stack development and in-house quality assurance. The AUT working group is currently working on expanding the tester in order for it to be capable of certifying protocols and features in the area of TSN (Time Sensitive Networking).
PROFINET controller certification:
After the successful establishment of the certification system in the device certification subproject, the mandate was extended in 2018 to include the certification of PROFINET controllers. The provider-consumer model of devices and controllers, upon which PROFINET is based, posed a particular challenge. Where the Automated RT-Tester could still take on the active controller role for the certification of the devices, its basis has now been expanded so that it can initiate and evaluate test steps as a simulated device from an intrinsically passive position. 80% of the previously non-automated controller test cases have currently been implemented – the system is being continuously expanded to include additional test cases.
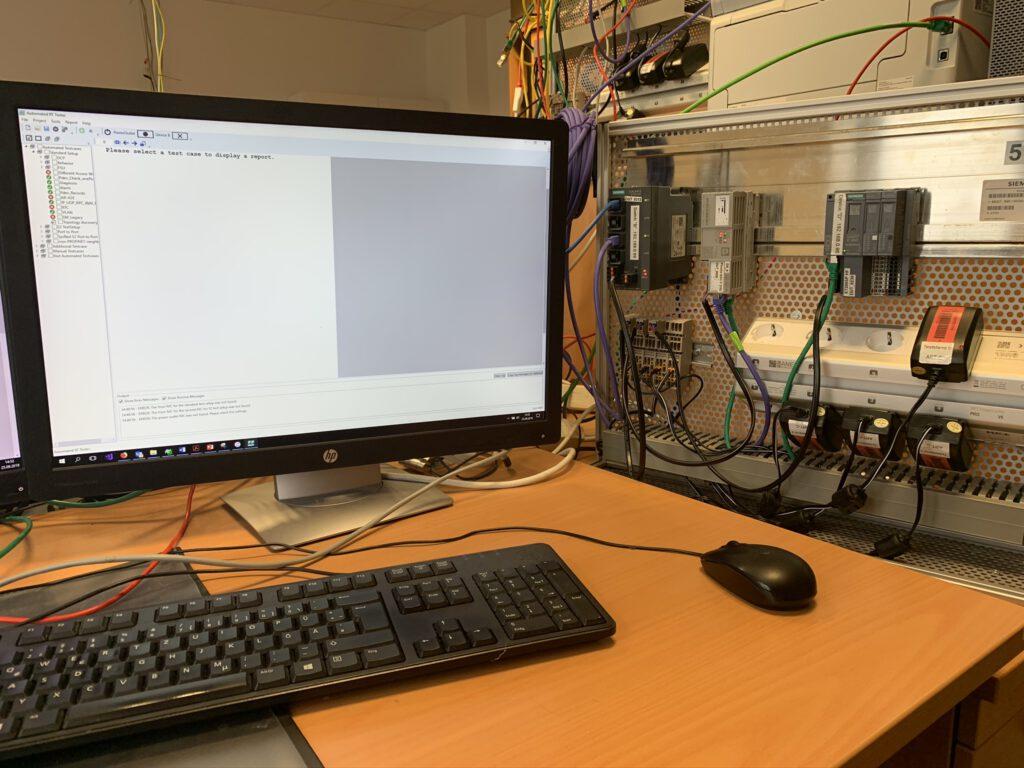
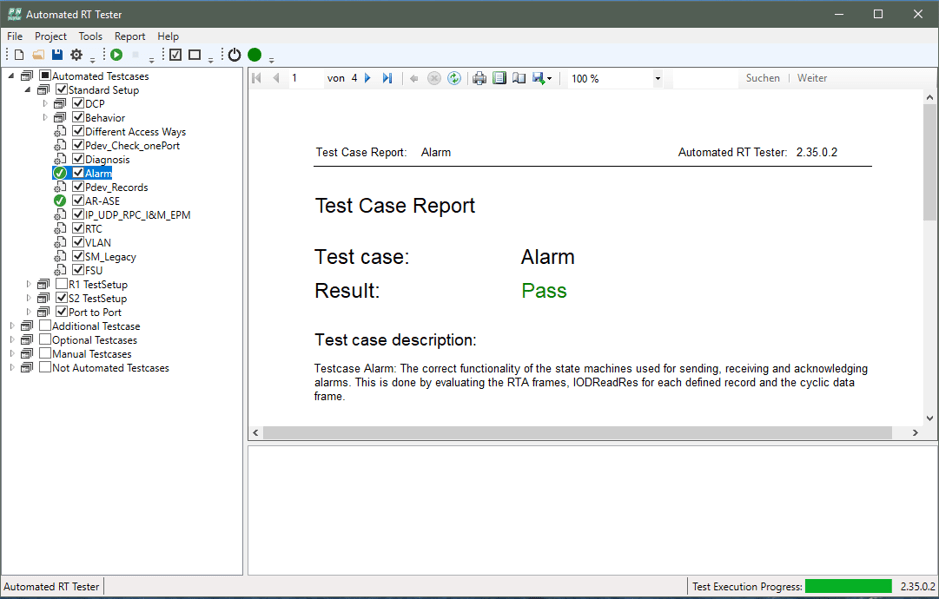
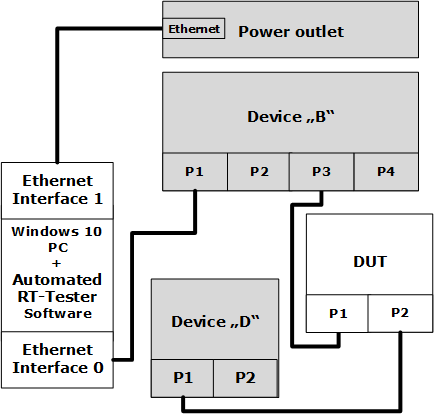
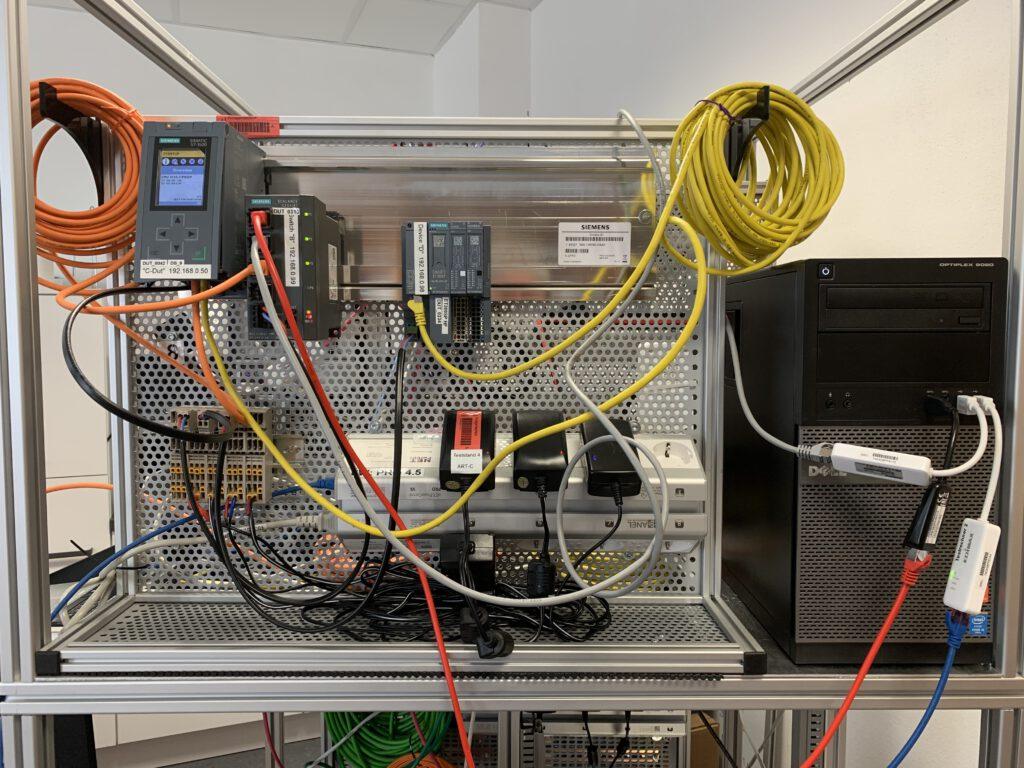
Testbed
In developing the certification test, we work closely with over 15 renowned manufacturers of industrial communication technology. Companies provide their devices (some of which are development samples), which are then used as part of the regular system and regression tests for quality assurance.
A test bed with over 50 different PROFINET devices and numerous PLCs was set up for these tests. There are currently ten test setups and ten DUT stands available; these are continuously updated to the latest hardware and firmware versions. 32 different devices from 15 different manufacturers are regularly used as development objects.
Devices from Bosch-Rexroth, Phoenix Contact and Siemens with the engineering tools Indra-Works, PLCNext and TIA Portal in the latest versions are used for the controller tests.
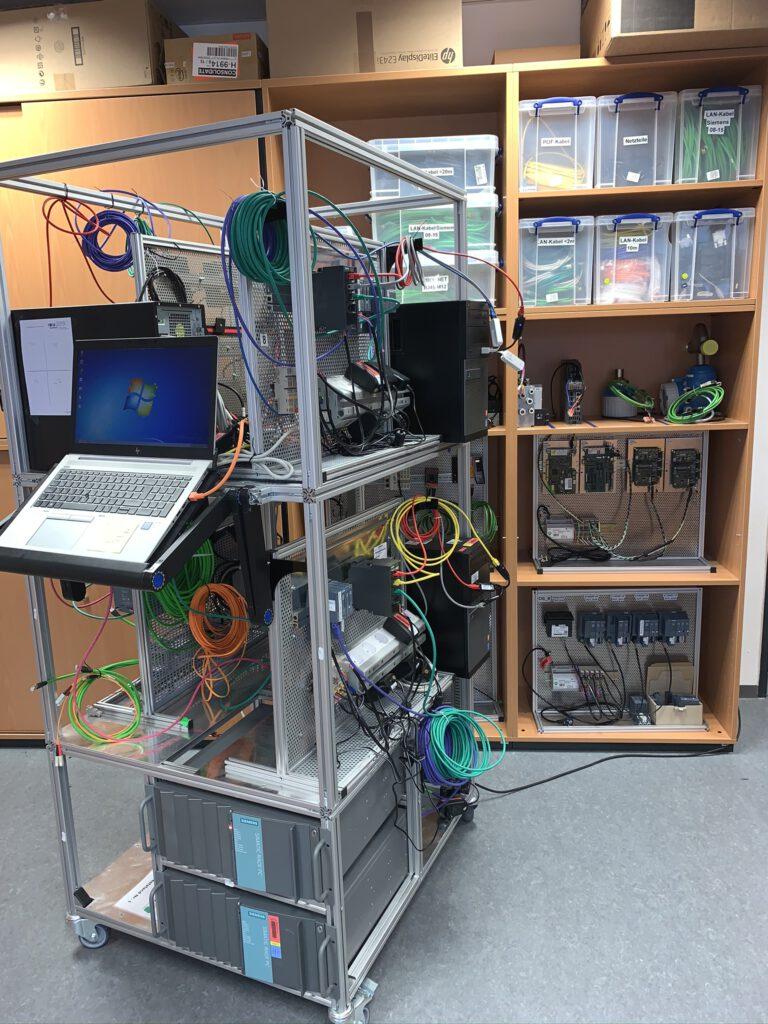
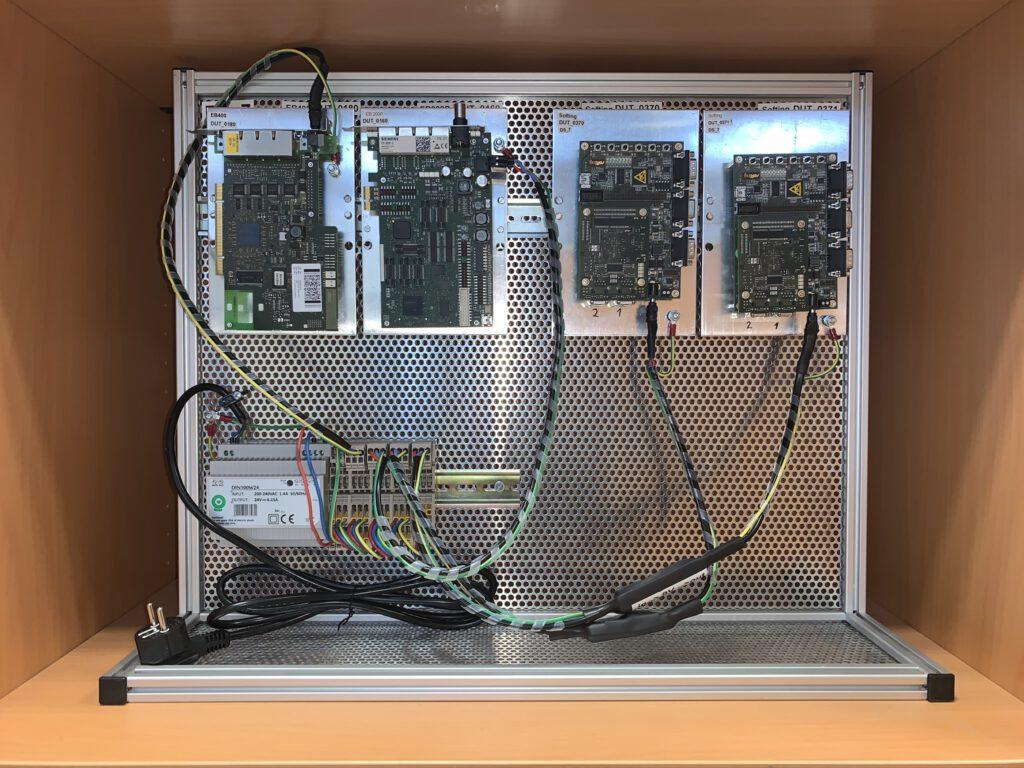
PROFINET @TSN
With the progressive realisation of Industry 4.0 scenarios, the requirements for networks in factories and production facilities are also changing. The increasing digitisation of industrial processes and the industry-related need for investment and future security require communication protocols that are supported by all established hardware and software manufacturers. And technical requirements such as reliability, real-time capability and isochronous operation are becoming increasingly important. Industrial protocols such as PROFINET are responding to this development by adapting their protocol stacks, among other things. Where previously proprietary solutions such as IRT (Isochronous Real-Time) were used on layer 2, in future TSN will also be available.
TSN (Time Sensitive Networking) refers to a collection of different communication standards on the link layer, which are now standardised by the IEEE and supported by a large number of manufacturers. Thus, there is justified reason to assume that TSN will spread rapidly in coming years, and gradually replace proprietary solutions.
This new strategy means a number of far-reaching changes for the Automated RT-Tester: new test cases must be specified and carried out in order to ensure the correct implementation of various TSN features in the certification process. In the long term, the increased requirements, especially in the area of isochronous communication, inevitably mean turning away from the currently established standard test setups. Therefore, a new test setup was designed in close cooperation with Siemens, and which allows time-critical processes to be outsourced to an external hardware component.
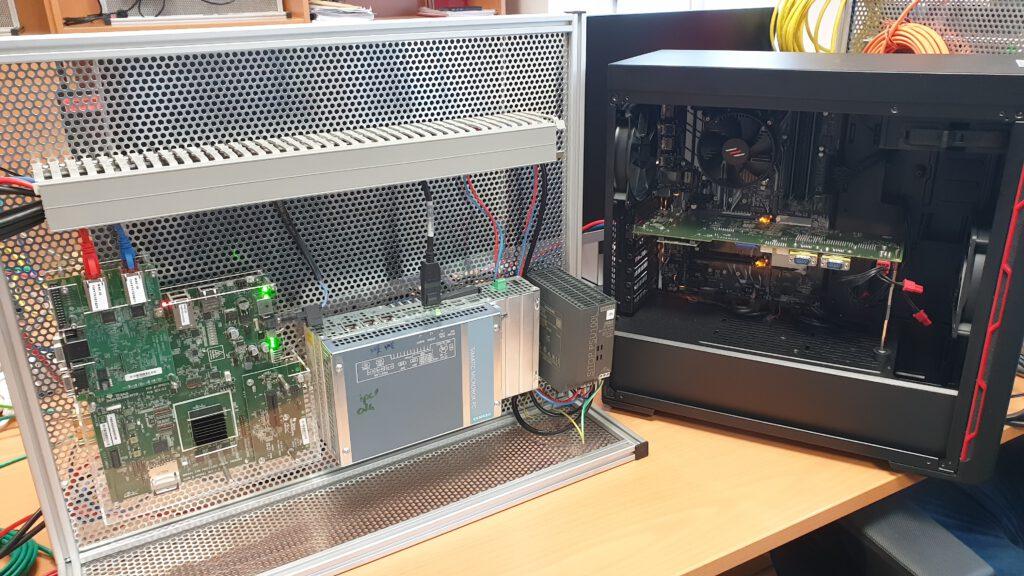
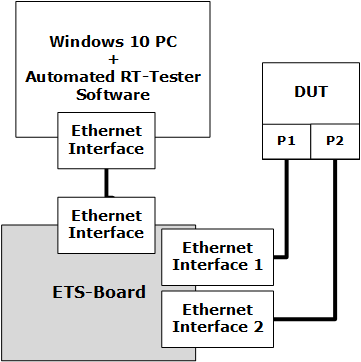