Labor Anlagentechnik System Test (LAST)
Die Ansprüche an heutige Automationstechnik steigen stetig. Hardware Komponenten, Leitungen und Kommunikationssoftware sollen Daten immer schneller umsetzen und trotzdem kostengünstig und kompatibel bleiben.
Um an effizienten Lösungen für diese Herausforderungen zu arbeiten, haben wir in unserem Labor an der OTH Amberg mehrere modulare Teststände aufgebaut.
Leitungssystem KoBus/KoBa
Im Projekt „KOBA“ wurden die Möglichkeit eines fortgeschrittenen steckerlosen aber leitungsähnlichen Backbonesystems für anreihbare Komponenten der Automatisierungstechnik untersucht und als Demonstrator aufgebaut. Weiter wurde gezeigt, wie dies für eine dezentrale Anordnung im Feld realisiert werden kann. Für diese Einsatzfelder sollte zum einen ein effizientes, induktives Energieeinkopplungsverfahren und zum anderen eine steckerlose robuste und zuverlässige Datenübertragung mit hoher Datenrate, aber geringer Reichweite realisiert werden. Gefördert wurde das Projekt vom Land Bayern.
Im Forschungsprojekt „KoBus“ (Kontaktloses Bussystem) wurde ein neuartiges kontaktloses Bussystem für die gemeinsame Übertragung von Energie und Daten in der Feldebene entwickelt. Das auf induktiver Übertragung basierende System sollte die bereits bekannten Vorteile einer kontaktlosen Übertragung wie eine hohe Flexibilität, einen geringen Wartungsaufwand und eine Beständigkeit gegenüber Korrosion bieten und dabei aber eine Vielzahl von Verbrauchern nicht nur mit Energie, sondern auch mit Daten versorgen.
Weitere bearbeitete Themenfelder rund um die kontaktlose Energie- und Datenübertragung sind die Auslegung und der experimentelle Aufbau von Pads für das Laden von Elektrofahrzeugen, unterschiedliche RFID-Applikationen und die kontaktlose Variante der GreenPHY-Kommunikation.
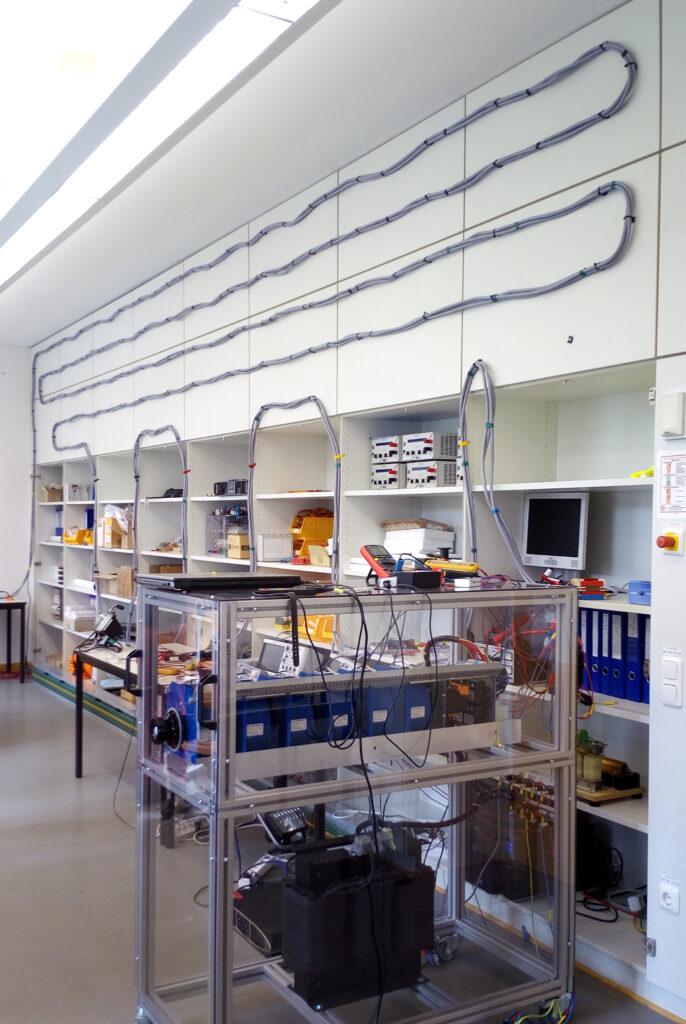
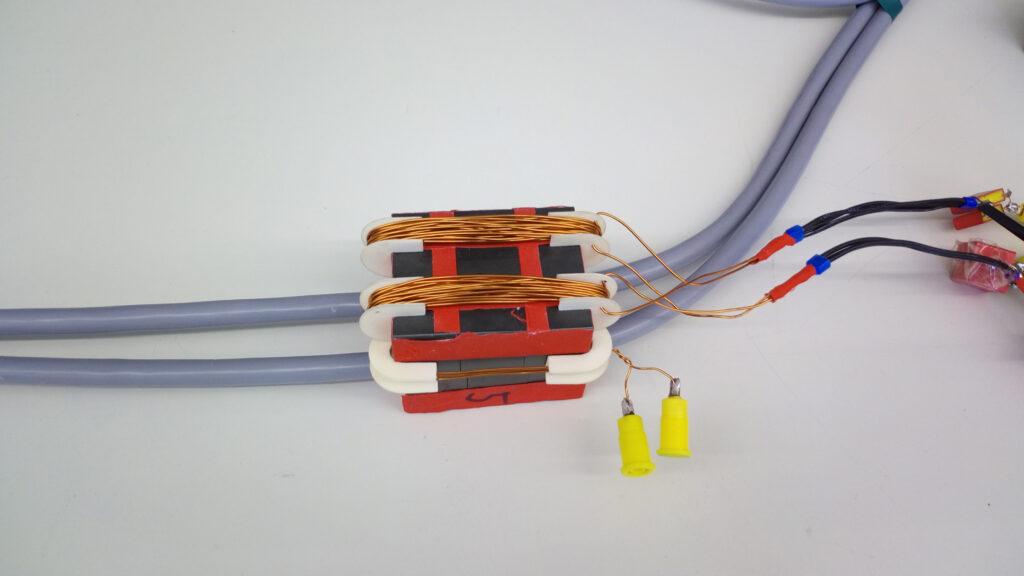
Smart Factory Demonstrator
Eine Reihe an Testständen wurde für das interdisziplinäre Projekt ISAC entworfen, um eine vollautomatisierte Prozesskette einer Industrieanlage zu simulieren. darunter fallen unter anderem mehrere Förderbänder, Motorstände mit Lastsimulatoren und Kommunikationskomponenten für Industrie 4.0 Anlagen. Mit dieser Simulationsreihe, soll ein Produkt, automatisiert weiterverarbeitet und in ein Lagersystem verfrachtet werden.
Die Besonderheit dieses Industrie 4.0 Demonstrators ist die modulare Bauweise. Acht voneinander unabhängige Fördermodule bilden die Basis des Demonstrators. Die Module untereinander erkennen sich über RFID. Durch die modulare Bauweise und die gegenseitige „Nachbarschafterkennung“ der einzelnen Module kann diese Anlage während des laufenden Betriebes neu angeordnet werden, ohne dass die einzelnen „Produktionsschritte“ der Werkstücke durcheinandergeraten. Die acht Module gliedern sich in zwei Gruppen. Modul 1 – 4 sind Querförderer. Sie haben keine Sensoren, aber einen Drehtisch der die Ausförderung in insgesamt drei Richtungen ermöglicht. Modul 5 – 8 besitzen Sensoren/Aktoren. Hier können die physikalischen Daten der Dosen ausgelesen werden, und eine „Bearbeitung“ stattfinden.
Weiterhin ist in Modul 6 und 8 ein Motorenprüfstand, bestehend aus einer ASM und einem Servomotor eingebaut. Mit ihnen können nicht nur realistische Störungen auf der Datenleitung erzeugt werden, sondern auch die aktuellen Messwerte (Drehzahl, Drehrichtung, Drehmoment) dynamisch an die SPS übermittelt und auf der HMI visualisiert werden. Dieser Motoren befinden sich zurzeit im Aufbau.
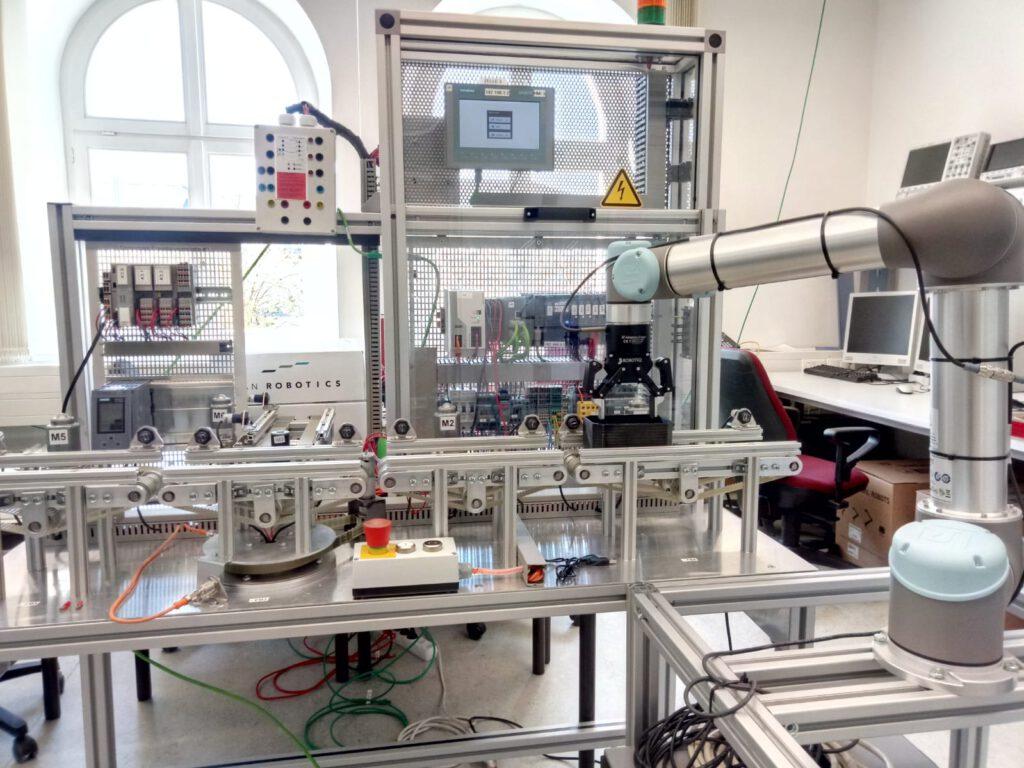
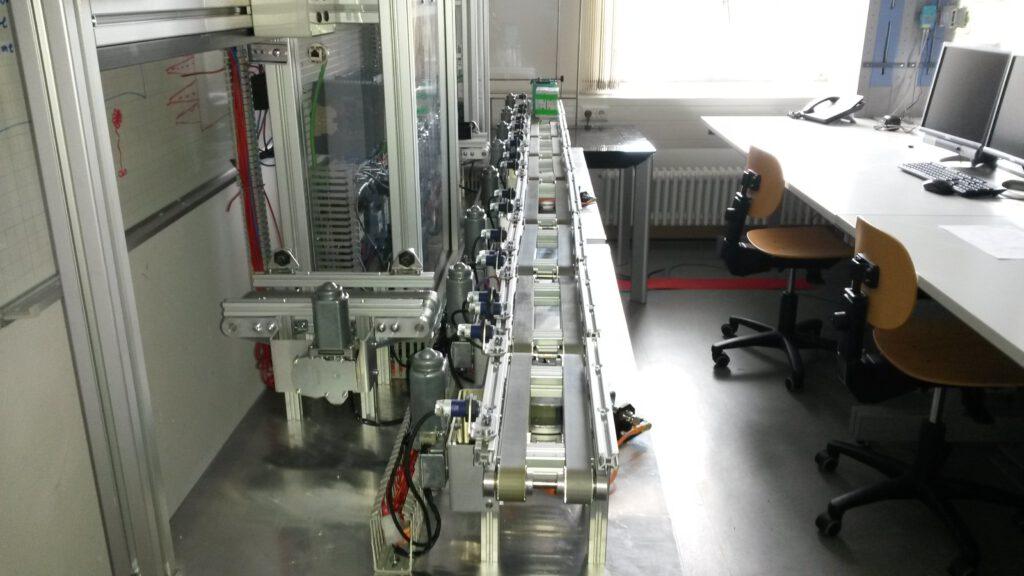
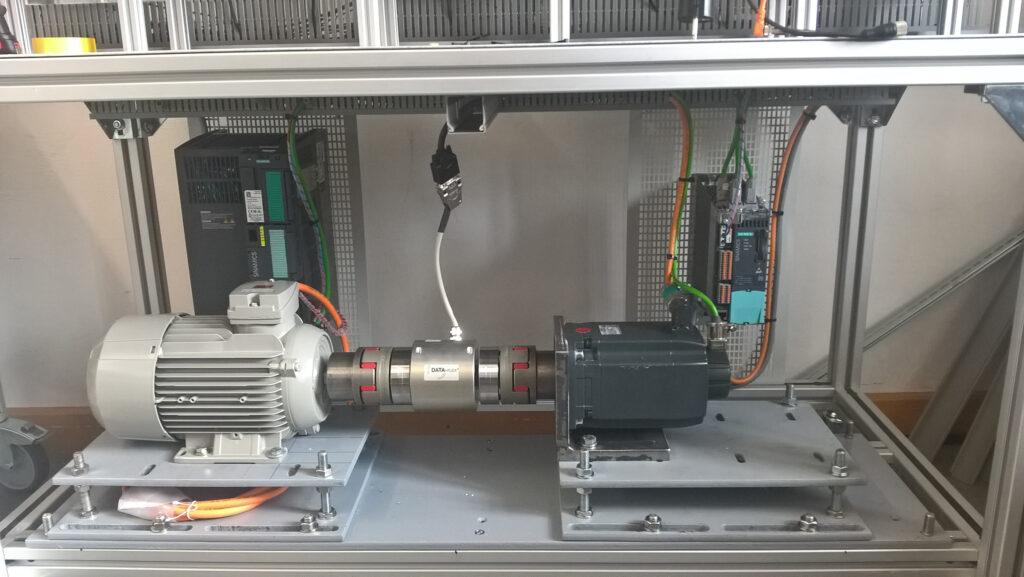
Industrielle Kommunikationstechnik und Automatisierungssysteme
In den Vorlesungen erhalten Studenten einen Einblick in die Prozessautomatisierung und die dafür notwendigen Komponenten und Systeme. Dazu werden Kommunikationssysteme zur Prozessdatenübertragung (PROFINET, Ethernet, …) sowie Echtzeit-Betriebssysteme und Echtzeit-Anwendungen zur Prozesssteuerung behandelt.
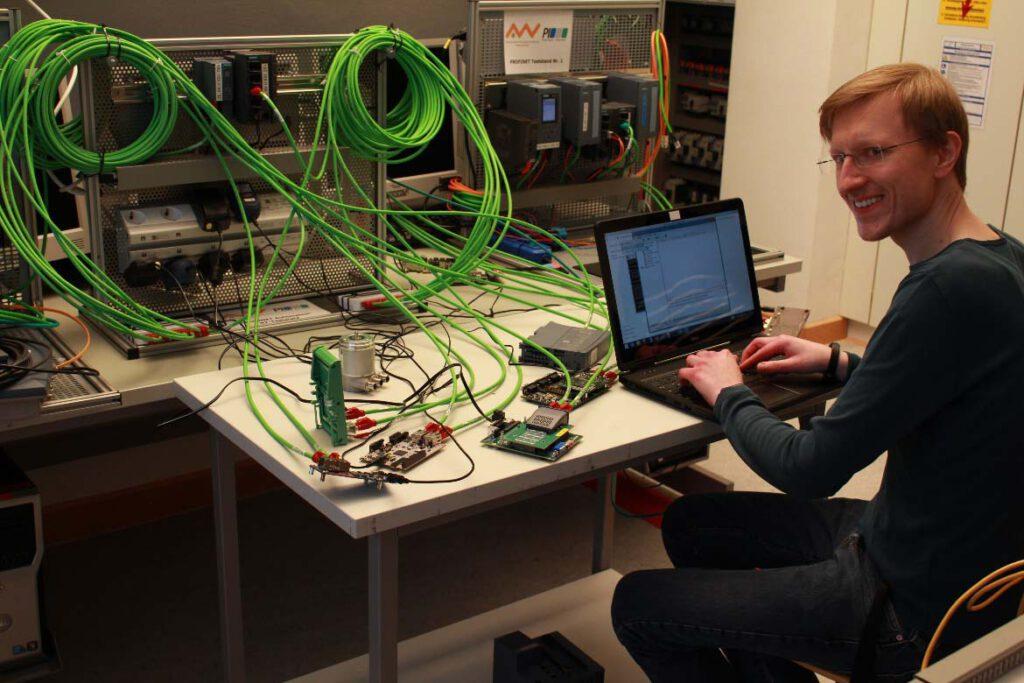